Customized service
Standard service process
CHG Bearing is dedicated to providing professional solutions for every client!
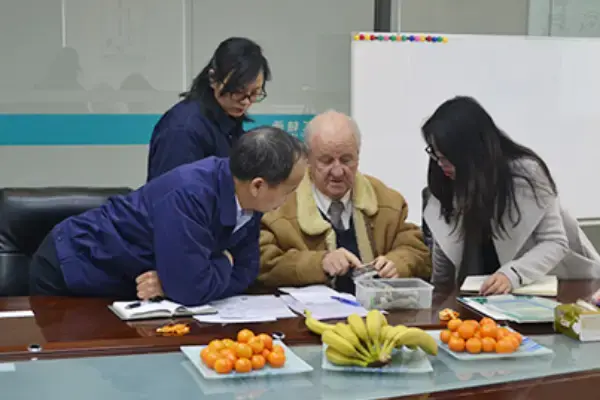
1. Demand analysis and communication
(1) Define customer needs: first of all, communicate with customers to understand their specific needs for bearings, including application scenarios, performance requirements, size specifications, material preferences and so on.
(2) Collect technical parameters: according to customer demand, collect the necessary technical parameters, such as speed, load, operating temperature range, lubrication, etc.
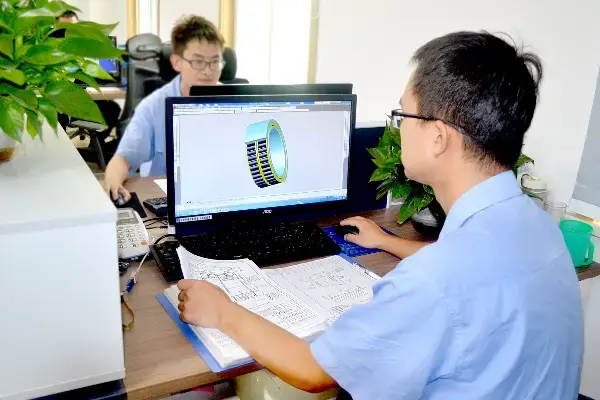
2. Design program development
(1) Preliminary design: based on customer requirements and technical parameters, the bearing manufacturer's technical team to carry out the preliminary design, including bearing type selection, structural layout, material selection.
(2) Customized drawings: draw detailed customized bearing drawings, including two-dimensional drawings and three-dimensional models, so that customers can review and confirm.
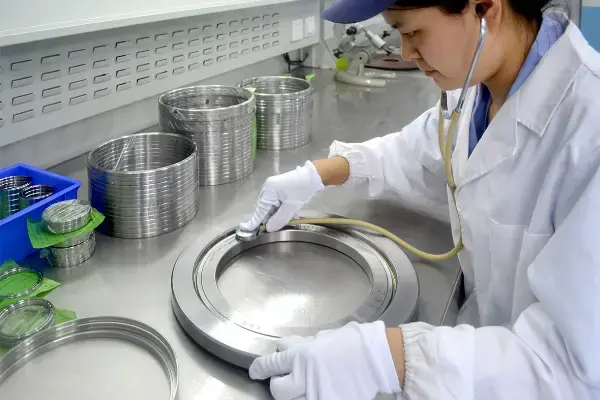
3. Sample production and testing
(1) Sample production: according to the design drawings, make samples of customized bearings.
(2) Performance test: conduct strict performance test on the samples, including load test, speed test, life test, etc., to ensure that it meets the customer's needs and performance standards.
(3) Customer feedback: feedback the test results to the customer, and make necessary adjustments and optimisation according to the customer's opinions.
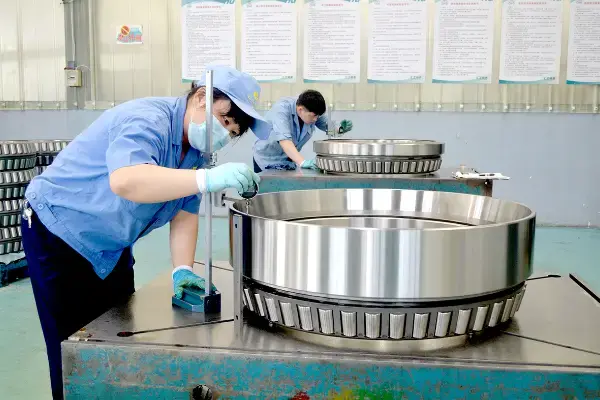
4. Mass production and quality control
(1) Mass production: After the sample test is passed, enter the mass production stage.
(2) Quality control: Strict quality control measures are implemented during the production process, including raw material inspection, production process monitoring, finished product inspection, etc., to ensure that the quality and performance of each batch of products meet the standards.
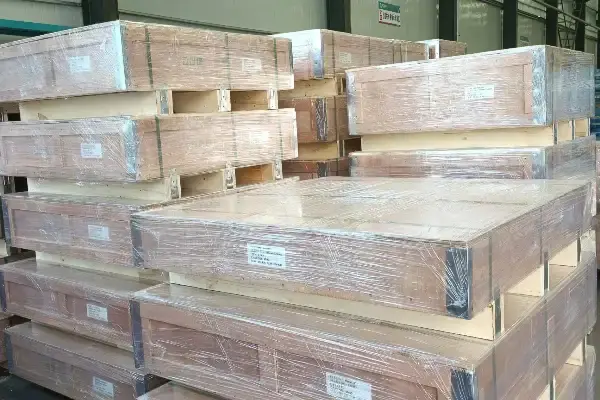
5. Delivery and after-sales service
(1) Product delivery: deliver the customized bearings to customers according to the agreed time and method.
(2) After-sales service: Provide perfect after-sales service, including installation guidance, use of training, troubleshooting, etc., in order to help customers better use and maintain the customized bearings.
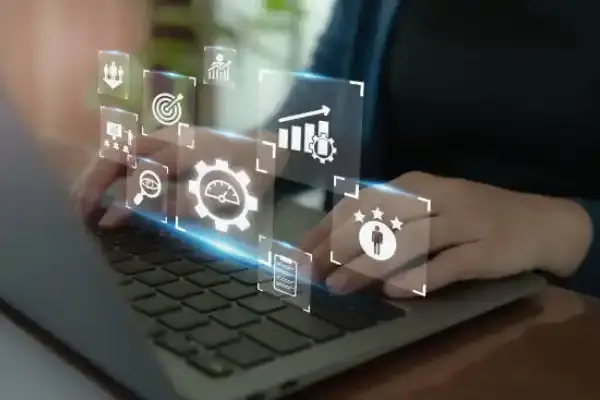
6. Continuous improvement and feedback
(1) Customer feedback collection: Regularly collect customer feedback on the use of customized bearings, including performance, service life, maintenance costs and other aspects.
(2) Continuous Improvement: According to customer feedback and market demand, we continuously optimise product design, production process and service process to enhance customer satisfaction and market competitiveness.